Resistance welding guide (parameter study, stable operation)
In this article, I'm going to talk about the topic of "Resistance welding guide". In production engineering, various methods are used.
Among them, resistance welding, which is used for joining the energized part of the product, will be explained based on my experience as a production engineer, focusing on the initial parameter verification and key points for mass production.
In the process of welding, the control items vary greatly depending on the place and purpose of use. Detailed control is not necessary if the welding is performed on non-quality critical parts.
In this article, I will use the condition that welding is introduced into the metal joining of energized parts. The joining of energized sections requires extremely high quality standards.
【content】
- What is resistance welding?
- Introduction of metal-to-metal connecting methods
- Initial Evaluation of Resistance Welding
- Welding Parameter Evaluation
- Quality evaluation of welding
- Quality considerations at resistance welding process
- Concerns about resistance welding process in mass production
- Terminal shape
- Electrode heat generation
- Durability of welding electrode and quality of welding electrode
- Electrode cost
1.What is resistance welding?
As shown in the figure, the principle of resistance welding is that a large current is passed through a metal terminal under pressure between electrodes and heat is generated by the resistance of the contact area. This process is used to melt and fix the metal terminals by applying pressure in this state.
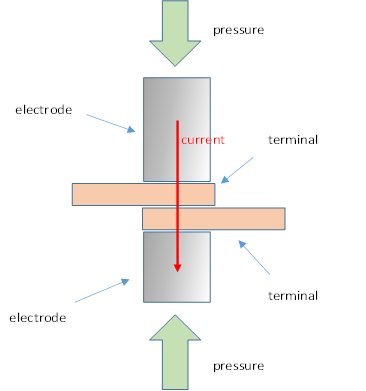
2.Introduction of metal-to-metal connecting methods
In addition to resistance welding, metal-to-metal joints can be made by arc welding (the kind of welding you generally think of when you hear the word "welding") , press-fit, caulking and soldering. Each has its own advantages and disadvantages.
Press-fit or caulking, which requires only a mechanical connection, is used to join metals in areas where there is no current flow.
These methods are simpler than welding and soldering, and quality control is easier.
On the other hand, the energized areas are often shaped like molded metal terminals and generally lack mechanical strength. These areas are welded or soldered.
Arc welding melts metal using the principle of lightning strikes, so fine control is difficult and the electrodes are not durable.
With soldering, the process itself is simple, but there is a risk of solder balls getting mixed in, and there are issues with reliability at high temperatures.
For this reason, resistance welding is used to join energized areas.
3. Initial Evaluation of Resistance Welding
From here, this is job for production engineers.
An initial evaluation must be done before installation.
The welding parameters are evaluated prior to sample production in the prototype phase. The same applies to the mass production process. Once the mass production equipment is complete, The welding parameters are verified again before production begins.
It depends on the environment in which the product is used, but in order to guarantee the durability of energized parts at high temperatures and the strength to withstand external shocks, it is not enough to just have electrical continuity in weld part.
In addition, the quality of the parts related to functions such as electric energized parts often have special characteristics and require a higher level of quality control than normal process.
And it is the production engineers who set the standards for this control.
The following are the items to be verified.
Since there are many items, I will explain them with specific examples.
<parameter evaluation items>
Pressure, welding current, welding time, displacement, welding electrode
<Quality judgment items>
Weld strength, cross-section
Welding Parameter Evaluation溶接パラメータ評価
Select about three different pressures to be applied.
Based on the size and shape of the metal terminal, you can have the manufacturer of welding equipment make a guess, or you can refer to the parameters of similar models.
At each pressure, perform the following matrix evaluation with the welding current and welding time.
A rough determination of which conditions are stable is made.
※In the matrix below, blue is OK and red is NG.
The items to be judged are the amount of displacement and the appearance of the weld.
The criterion for judging the amount of displacement will be described later.
The appearance of the weld should be determined based on the relationship between the degree of melting and the weld strength.
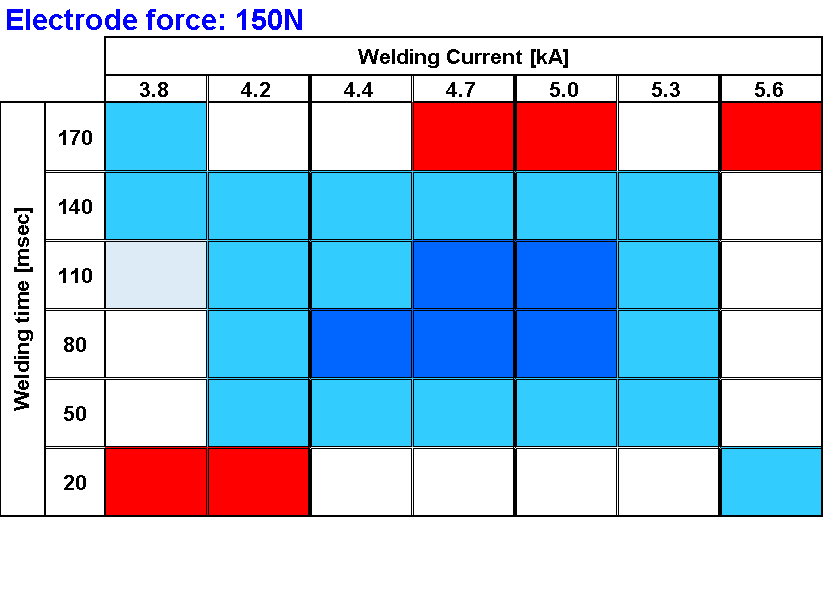
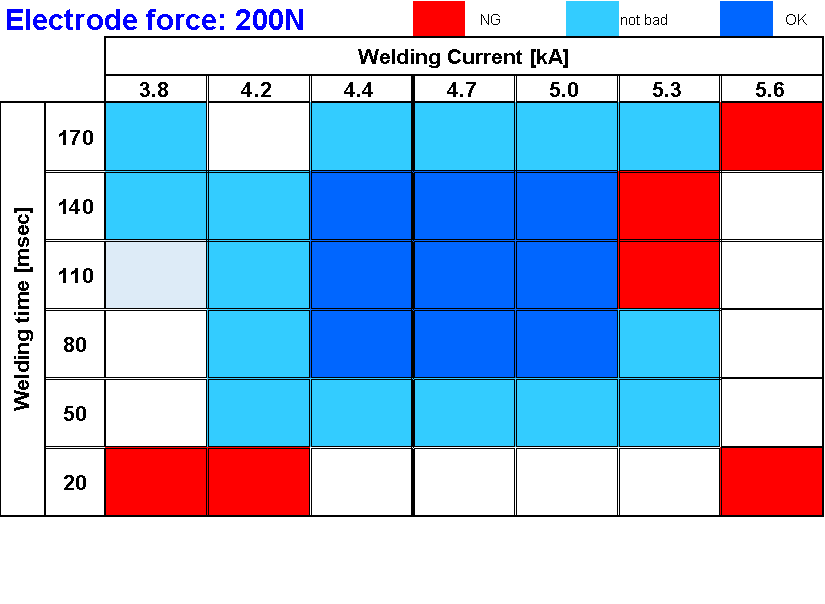
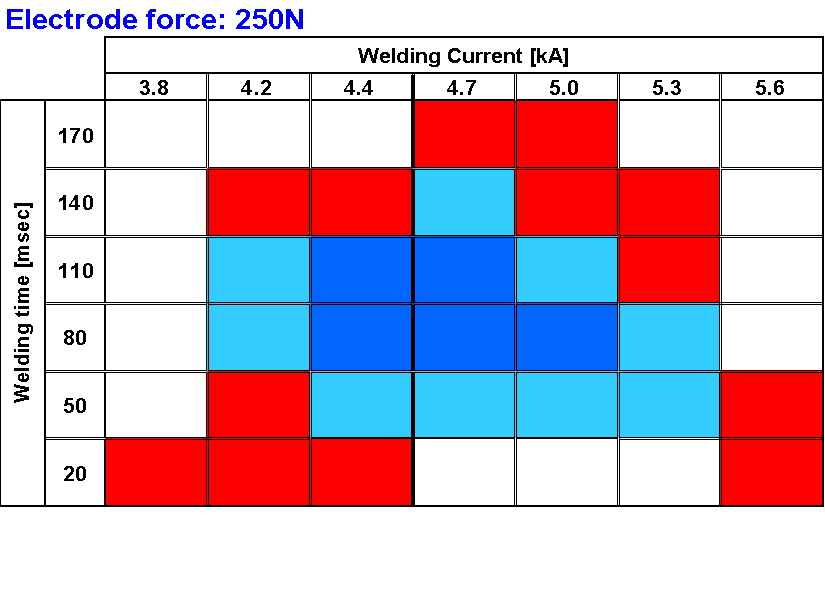
A more detailed investigation is carried out using a force that ensures a wide range of stability parameters. In the example above, the stability range is wide when the applied pressure is 200N, so the detailed parameters are determined in the blue zone with the applied pressure of 200N.
Quality evaluation of welding
The next step is quality evaluation. The weld strength of the samples made for each welding condition is measured. The relationship between the weld strength and displacement is shown in the graph.
As shown in the graph, the weld strength increases as the amount of displacement increases, and once it reaches a certain point, the weld strength does not change.
If the displacement is increased beyond this state, the weld strength will decrease. As you can easily imagine, the point at which the weld strength drops is that it is over-melted.
While taking into account the safety factor of joining the terminals, the load and durability on electrodes, the adequate welding conditions are those with a displacement of 0.5 to 1.0 mm.
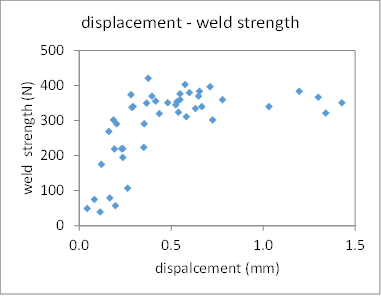
The welding conditions have now been determined.
The next step is to make a series of samples with the same parameters and evaluate the process capability for displacement and weld strength.
If the process capability is acceptable, this completes the initial evaluation.
This can be a time-consuming and tiresome task, but it is within the scope of production engineer's job.
Quality considerations at resistance welding process
Welding and soldering are difficult processes in which it is difficult to make quantitative judgments about quality. Unlike the press-fit and inspection processes, these processes do not have specifications and cannot be judged numerically. It is only indirectly judged by the appearance of the weld and the displacement of the welding electrode.
(Quality can be checked directly by destroying the weld part, as in the case of weld strength inspection and cross-section cutting.This can only be done by sample inspection)
Therefore, reliability of the process parameters during welding has a great effect on quality. If this fact is not properly understood, serious quality problems can occur during mass production.
4.Concerns about resistance welding process in mass production
Next, let's move on to the key points of the mass production process.
Problems that are not considered in the initial verification process occur during mass production, and I will introduce some examples of such problems.
Terminal shape
One of key factors that stabilize resistance welding is the shape of the terminals. Welding is relatively stable in the case of two flat surfaces, but if one of the terminals has a round or spherical shape, it is disadvantageous to the stability of the contact area with the electrode.
This shape can cause problems such as accelerated wear on the electrode surface and unstable contact resistance, resulting in unstable displacement.
The shape of the terminals depends on the product designed by R&D department, but the production engineers need to input information because the people in charge of product design do not know anything about welding process.
If necessary, a terminal shape should be suggested at an early stage.
Electrode heat generation
The electrodes become hot during continuous use, and the resistance inside the electrodes affects the welding operation.
A cooling chiller is used for the mass production process, but the cooling capacity varies depending on frequency of continuous use, so it is necessary to correctly determine the cooling capacity.
Lack of cooling capacity can affect the quality of the weld, but it can also raise an alarm on the cooling chiller side and prevent mass production.
These things happen unexpectedly. In the initial stage, it is difficult to detect problems because of the small number of production volumes, but after full-scale operation, it is often the case that the cooling capacity is insufficient.
Durability of welding electrode and quality of welding electrode
The next step is the durability and quality of the welding electrode.
Depending on the frequency of use, the electrodes may need to be changed or polished several times a day during full-scale operation.
If the electrode quality is not good, the weld will not be stable after electrode replacement.
Since the same electrodes were used at the time of initial evaluation, problems that were not found until mass production appear when the electrodes are replaced.
The welding electrode is made of tungsten and copper.
Depending on the contact state and resistance between tungsten and copper inside the electrode, it can affect the operation of resistance welding.
Electrode cost
Finally, there is the electrode cost.
As mentioned above, you will be spending a lot of money if you are replacing them multiple times a day. Lowering the unit cost of the electrode will have a significant effect in the long run.
It all depends on the initial consideration such as electrode shape. It is important to propose less expensive shape, or if you can use welding electrode of existing model, you should adopt a plan to use the same electrode instead of making new electrode at early stage.
These are the key points about resistance welding from initial evaluation to mass production.It is summarized from the perspective of a production engineer.