Correlation study for test equipment by production engineers
In this article, I will talk about the theme of "Correlation study for test equipment by production engineers". Test equipment must be highly reliable. Before installation, there are several items that must be evaluated. In this article, I will outline one of them, correlation evaluation.
【content】
- What is the correlation of test equipment?
- Examples of Correlation study
- Key points of Correlation study
- How to select a sample, quantity
- How to do it when the master equipment is far away
- Aligns the basic specifications of test system with master system
- It may have to correlate with the customer's test equipment...
- Bad cases I've seen in the past
- Correlation study of multiple testers all together
- Aligning tester with the numerical results of the master sample alone
- Not even a correlation study was done in the first place
What is the correlation of test equipment? 検査装置の相関とは
The test equipment must be reliable in its judgment results. These include repeatability, linearity and correlation. Correlation is measure of the reliability of the results, even when measured by different test equipment.
For example, suppose there is scale A and scale B. When the weights of a person weighing 40kg, 50kg, 60kg, and 70kg are measured on each scale, the results are as following
- Scale A: 41, 51, 62, 73
- Scale B: 40, 50, 60, 70
In this case, at around 40-50kg, both scales are close to each other, but at 70kg, there is a 3kg difference.
This makes it hard to know which is the more reliable value.
Correlation of the test equipment is simply an evaluation item that shows whether or not it shows a similar trend for the master equipment.
Examples of Correlation study
Here is one concrete example. This is the value of resistance and inductance of coil. The value of the master test equipment is recorded on the horizontal axis and the value of the slave test equipment on the vertical axis.
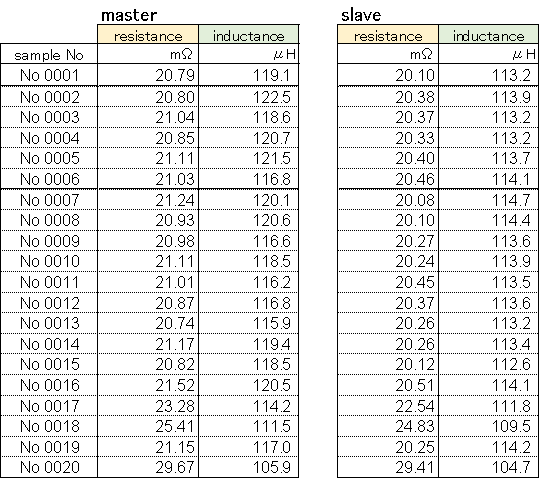
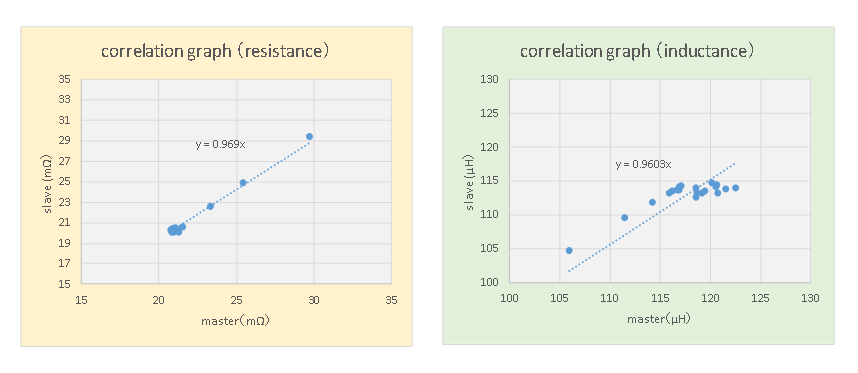
Test equipment on the master side is generally used in development centers, such as test benches.
This is because they are considered to be the most reliable test equipment.
The slave test equipment (the test equipment to be evaluated) is the test equipment for mass production facilities or new test equipment to be introduced.
※For mass production equipment, fine tuning of positioning and control is often difficult due to the simplification and automation of loading/unloading methods, and generally the inspection accuracy tends to be less accurate than that of test bench.
In this case, two items were evaluated simultaneously, but depending on the test equipment, the number of test items could be 10 or more.
Correlation of all those items must be achieved.
Key points of Correlation study
Here are a few points for evaluation.
Correlation values can be easily calculated from two groups of data by using Excel's correl function.
How to select a sample, quantity
Depending on the item being tested, I recommend using about 30 samples to increase the reliability of the validation results.
Also, samples that have wide distribution of data within specification should be used. A sample group with less data variability will not produce good correlation.
※Look at the above graph and consider the case where the data distribution is small. You can't run an approximation curve, can you?
How to do it when the master equipment is far away
The fact that there is no master test equipment at the same site does not mean that you do not have to perform correlation study.
It is common practice to send samples tested at one site to the other site and compare the results of the two tests to confirm the correlation.
To avoid difficulties later, prepare samples for correlation study while the master machine is nearby and available.
When the new inspection system is completed, the samples should be shipped to the manufacturer's site for initial evaluation.
Aligns the basic specifications of test system with master system
High correlation cannot be expected unless the equipment and control system used are identical. There are some engineers who decide the specifications of the inspection system without doing preliminary research, but they have a hard time after the inspection system is completed. It is so important to keep the basic specifications of the test equipment consistent with the master machine.
It may have to correlate with the customer's test equipment...
Depending on the product characteristics, it may be necessary to correlate with the customer's inspection system.
However, as mentioned above, correlation evaluation is not so easy.
It would be nice if the specifications of the customer's test equipment were similar to your own, but in most cases this is not the case.
If a problem occurs on a customer's production line with some characteristic, the reliability of your company's inspection process can be questioned.
When these problems occur, the customer may come on board and it can be quite troublesome.
If you have the right processes in place and you have the right test equipment in place, there's nothing wrong with that.
If you have implemented poor process, you will have to start all over again.
Bad cases I've seen in the past
As an engineer, I have the opportunity to see other people's work, and I would like to share some of the unbelievable statements that some veteran engineers made.
Correlation study of multiple testers all together
The idea was to correlate several distant test equipment with the master system in the development center. Moreover, there were more than 10 test items on that inspection.
It would be difficult to fit just one of them together.
It's impossible for someone who knows the operations to run and evaluate multiple test equipment in parallel.
But that person was a manager, and he didn't mind saying that.
In addition, if one device (device A) at another site (base A) is correlated with the master device at the development center, then the correlation study at base A can be done by treating device A as the master.
It is not necessary to use the master unit in the development center as the master each time.
Aligning tester with the numerical results of the master sample alone
A common mistake is to adjust the inspection machine based only on the results of the master sample. This results in a small data distribution and unreliable linearity. This is a common mistake made by engineers who do not understand correlation evaluation at all.
Not even a correlation study was done in the first place
This is also unbelievable in terms of the introduction of test equipment, but examples like this exist in workplaces that are overwhelmed by work.It is also common in workplaces where there are few experts.
Depending on the products you handle, you may not need detailed evaluations.
People from other industries may not even be aware of this in the first place.
RELATED) Production Engineering Job Descriptions and Career Development
RELATED) Work Quality and Schedule control of Production Engineer
RELATED) The need to properly understand the essence of problem and common misunderstandings