Introduction of caulking process and common misunderstandings
In this article, I will talk about the theme of "Introduction of caulking process and common misunderstandings".
Various methods are used in production engineering. Based on my experience as a production engineer, I will introduce the caulking method and key points for mass production.
The caulking process can be as simple as using crimping tools, or as large-scale as using a hydraulic or servo press. I will focus on the latter this time. In terms of process overview, the following figure shows an example of mass production equipment.
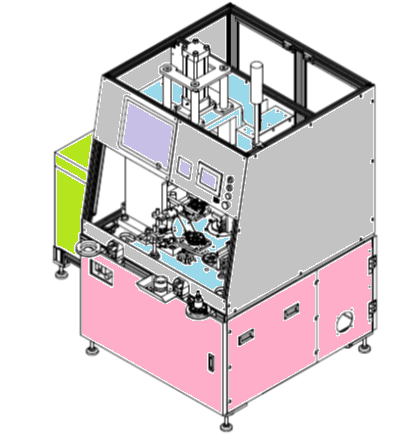
【content】
1.What is caulking
To begin with, caulking is a method of holding a rigid metal component.
Press-fitting and caulking are common methods of holding rigid metal component, and they are both similar.
While press-fitting is a method of pressing a part under press-fit tolerance, caulking is a process in which load is applied to rigid body after the other component has been assembled by insertion fitting.
For example, let's say you want to caulk a bearing into an aluminum housing.
After inserting the bearing into the aluminum housing, caulk the edges of the aluminum housing.
2.How to control caulking properly
The caulking control method is to apply constant load for a certain amount of time to deform the product.
The way it works is to judge the load at stable end. The load graph is shown below. It is very simple.
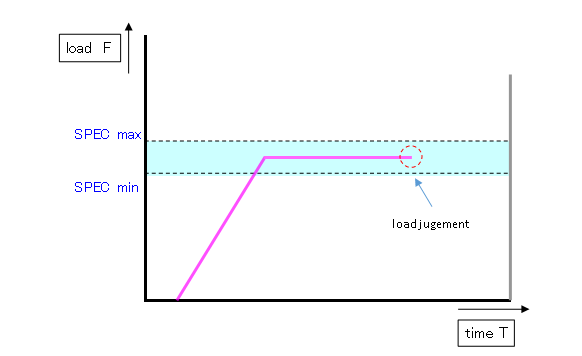
3.incorrect caulking control カシメの間違った制御方法
In rare cases, there is equipment that incorrectly controlled as following. When a certain load is reached, the load is stopped and terminated. The waveform is as follows
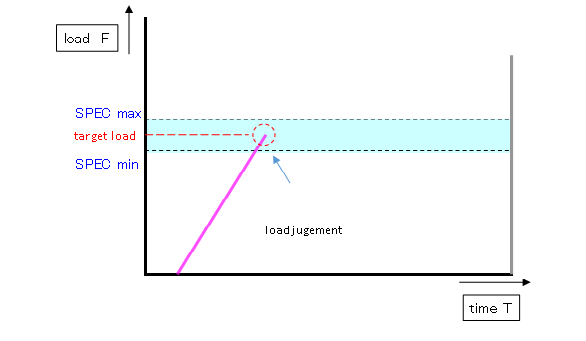
Since you can control the equipment in any way you like, you can also adopt this control method. In this control, the load arrival signal of load cell is taken as an input signal and the press operation is stopped.
There are two problems.
The apparent load is indicated correctly, but actual load is unknown.
Depending on the responsiveness of the control equipment.
It means that the product is loaded more than expected.
For example, as a control to stop at 10,000 N. Let's say, the press capacity is set at 30,000 N. Even if indicated load on display is 10,000 N, the actual load may be up to 15,000 N momentarily.
There are surprising numbers of production engineers who use this kind of press control without realizing it.
4.Caulking quality control
The judgment items at the equipment side are load and stroke. However, these are just judgments for equipment operation.
It is not possible to tell whether quality of the product is correct or not from the judgment results of equipment.
The appearance of the caulking part, caulking depth, and pull-out load can only be determined by looking directly at product side.
The purpose of caulking is to hold parts together. Loss of retention force due to vibration or impact is a serious functional failure of the product.
No matter what the product, the parts that require caulking (i.e., where parts are required to be fixed) have special characteristics. Therefore, more severe quality control is required than normal process.
This includes control of caulking depth using control charts and monitoring of pull-out load by periodic destructive tests.
5.Stroke management
Some equipment is installed with linear gauge to measure the caulking depth.
Depending on what measurement method is used, the reliability of the dimensions can vary greatly.
For example, if linear gauge is placed underneath the press to determine the lowering position of the press when it is lowered, this is just a reference value.This means that it is impossible to measure the caulking depth correctly.
Caulking depth cannot be measured because it is affected by height tolerance variations in the product being set. What you can measure is the reference value of where the press has gone down to.
To measure the caulking depth accurately, servo press or similar device must be installed to capture the press stroke from the coordinates where the caulking load is applied to the final caulking position.
In this case, this is a reliable measurement.
6.Concerns in mass production
The construction method itself is simple and the process is easy to operate stably. Nevertheless, daily quality control and periodic replacement are necessary because of the wear and tear of these parts. In addition, the quality of the caulking tools must be carefully monitored, as changes in caulking tools can greatly affect the quality of the caulking process.
Wear and tear of caulking tools
The caulking tool is made durable by material selection and hardening treatment. However, it is a consumable part and must be replaced periodically.
It is common to control the number of shots with counter on the equipment, or to determine the control range based on the trends in the caulking depth control chart, or to determine when to replace by periodically looking at the trends in the pull out load of caulking part.
Not managing anything is too risky.
Caulking area
If the contact area of caulking tool changes, caulking quality will change even with the same equipment parameters. As you can see, (pressure) P = (load) F / (area) S.
This is because the final pressure on product will change even if the press load is the same. As a result of increasing or decreasing of contact area of caulking tool, the caulking depth may be shallower or deeper.
For important parts of the caulking tool, it is necessary to carefully check the drawing to ensure that the dimensions are specified correctly.
Also, when the spare tool is completed, it should be carefully checked to ensure that it is finished to the correct dimensions.
7.Advantages and disadvantages of the caulking method in mass production
The method of caulking has a great advantage in terms of material cost, as it allows for fixation of two parts by simply applying load. The caulking method itself is not difficult.
If you don't use caulking, you'll need an additional fixture, such as a screw or retaining ring. It's easy to imagine the impact in terms of material costs.
On the other hand, one disadvantage is that it cannot be disassembled. The assembly process of caulking is a completely irreversible process. So if you try to disassemble it later, it's impossible unless you destroy.
For example, if something goes wrong and you end up with a large amount of defective inventory, there is no way to rescue them.
For products that are unstable in terms of defect rates and other factors (i.e., products that are likely to disassemble), it may be best not to use the caulking method.
The other is the risk of metal particles. Since this is a method of deforming metal, metal chips are generated before and after the operation.
There is little to worry about when caulking aluminum products, but when caulking steel products, the risk of damaging the caulking tool must be considered.
Even if a part of tool is missing, there is no chance of detecting it by load or stroke, which can cause serious failures as metal chips can enter the product.
These are the points that production engineers should pay attention to when using the caulking method
RELATED) Lowering capital investment requires technical skills
RELATED) Overview of vision system (Principle of edge detection)
RELATED) Introduction of resistance welding