Job Descriptions of Each Department in Manufacturing Industry(Focus on the negatives)
In this article, I will be talking about " Job Descriptions of Each Department in Manufacturing Industry".
For those who are considering joining manufacturing industry, or who are already working in manufacturing industry and are considering moving to a different department, I will provide an overview of the work of each department from the perspective of production engineer.
The colorful parts are advertised in the world, so I'd like to focus on the negative parts of this article.
*I'm going to be as objective as possible, but please refer to it as a production engineer's perspective.
【contents】
- The overall work flow in manufacturing industry
- Stage 1: New product promotion
- Stage 2: Official nominations for the project
- Stage 3: Preparing for mass production
- Stage 4: Mass production begins
- Introduction of each department job (Product Design Department)
- Introduction of each department job (Purchasing Department)
- Introduction of each department job (Production Engineering Department)
- Introduction of each department job ( Manufacturing Department)
- Introduction of each department job (Quality Assurance Department)
The overall work flow in manufacturing industry
Before introducing each department's job description, let's take a look at the overall work flow in manufacturing industry (B to B). The following table summarizes the roles of each department in four stages.
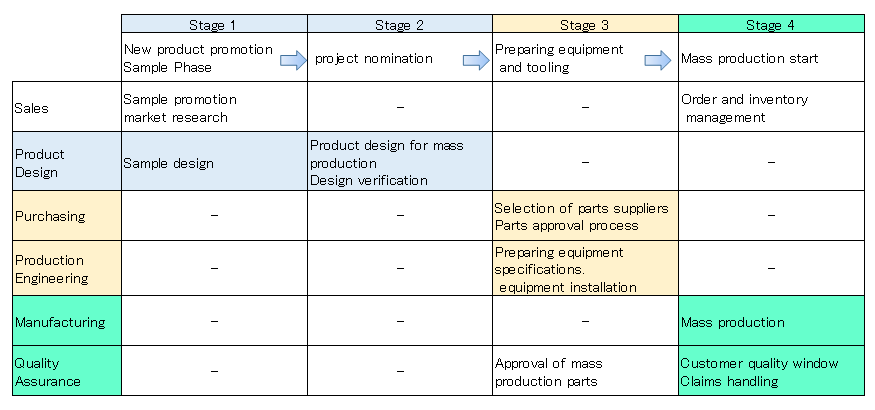
Stage 1: New product promotion
In this stage, a product sample is prototyped according to the specifications required by the customer. If the customer is satisfied with the price and characteristics of the product, we move on to stage 2. The activities in this stage are mainly those of Sales Department and Product Design Department.
Stage 2: Official nominations for the project
Once we receive formal nomination for the project from customer, we begin preparations for mass production.This is the design verification stage, which includes detailed product design and reliability testing.
The number of samples is increased from Stage 1 to confirm feasibility of mass production and product characteristics. Again, the Product Design Department takes the lead in these activities.
Stage 3: Preparing for mass production
Once the product design validation process is complete and the product design is fixed, the activities to prepare for mass production begin.
The role of the Product Design Department is terminated and the Production Engineering Department and Purchasing Department take over.
Production Engineering Department prepares specifications for the mass production equipment based on the product design and begins to introduce the equipment. Purchasing Department selects suppliers of product components and decides on prices and packaging specifications.
Production Engineering Department completes its work with the installation of the mass production line and process validation.
The Purchasing Department (Quality Assurance Department) is responsible for approving mass production (PSW) to the component suppliers.
Stage 4: Mass production begins
Once the stage 3 process is completed, the baton is passed to Manufacturing department.
They manufactures products according to the rules indicated in the drawings and manufacturing documentation. In the event of problems, they are supported by Product Design Department and Production Engineering Department.
Quality Assurance Department is responsible for quality and handling customer complaints.
Briefly, the above is the work flow in manufacturing industry.
Based on the above, here are some negative aspects of each department's job description.
Introduction of each department job (Product Design Department
Product Design Department is a popular department at all companies. You can feel your work taking shape and going out into the outside world, and you can acquire a high level of expertise, which is attractive in terms of career development and satisfaction.
Negatives in Product Design Department
In fact, this varies depending on the role and organizational structure.
The only stage where you can experience manufacturing is at stages 1 and 2.
Designing is mainly a desk job where you just draw pictures on computer or use expensive simulation software to analyze the data. In the case of mechanical design, they are busy just drawing and updating drawings.
When it comes to specialized areas such as electrical characteristics and functional characteristics, you need to spend at least three years of experience in the design department to be able to talk with experts.
Depending on the nature of the work, there are some people in the development department who have no understanding of product characteristics at all.
Depending on the company, the mass production line and the design center are located at different locations, so if you belong to R&D department, you will have a strange way of working, drawing product drawings without knowing the mass production process.
In the case of drawings for mass-produced products, main job could be just to update the drawings in response to requests from manufacturing factory.
So, although the colorful part is often emphasized, there are some negatives that you don't realize until you try it.
Introduction of each department job (Purchasing Department)
The main job of the Purchasing Department is to select suppliers and negotiate prices.
Even when they travel to suppliers, they are always in the position of "customer", so the word "business trip" is not associated with a bad image.
Material costs make up a large percentage of product costs, and it is a challenging and rewarding job because the efforts of the purchasing department can make a significant contribution to the company's profits.
Recently, business with foreign suppliers is increasing due to globalization. One of the privileges of Purchasing department is to be able to travel overseas easily.
Negatives in Purchasing department
Actual job also varies depending on organization.
The negative part is as following. Manufacturing department asks Purchasing department to deliver a replacement part as soon as possible, saying that problem from supplier component would stop production line.
There are also warehouse personnel who are in a hurry to make an order because the number of parts in stock does not match the physical inventory, despite the fact that the system shows that there are parts in stock.
And even though they have the power to negotiate prices, this is a trade-off with component design. If the drawing tolerances, characteristics and other specifications that come out of the product design department are too strict, the component price will not decrease.
Even if you are the buyer, in some cases the supplier may be in a stronger position than you. When you have no choice but to rely on that supplier, even the purchasing department cannot negotiate aggressively.
External factors, such as foreign exchange rates and metal market conditions, can affect prices, so prices may rise unexpectedly. They receive requests from internal management (or customers) to review our components prices in order to improve profits.
Introduction of each department job (Production Engineering Department)
(See other article for details.)
Production Engineering Job Descriptions
Introduction of each department job ( Manufacturing Department)
Next is the Manufacturing Department. This is the department that contributes the most to sales in manufacturing industry.
It is often thought of as simple work, but they have to work according to the rules and manage a large number of employees. It is also necessary to understand products and equipment, and it is a surprisingly hard job.
When you become an expert on the production line, you will be more familiar with product characteristics and equipment operation than useless engineer of engineering position.
Since many manufacturers in Japan don't have a manufacturing site in Japan, it seems that manufacturing-related personnel are rare.
Negatives in Manufacturing department
Now here's where the negatives come in.
There are problems on the production floor every day. Equipment breaks down, delivered components are faulty, or defects are found in the process.
Even if you ask the design department or production engineering departments to address the problem, sometimes they are not cooperative. They behave as if it were someone else's problem.
It's a miserable department that is overwhelmed with production, with many people not cooperating in a helpful way.
If you have quality problems, you are required to do additional inspections, which increases your work and reduces your productivity. ( Other departments have the idea of doing additional inspections on everything, which means more work on the manufacturing floor. )
In some cases, they are forced to produce "difficult-to-assemble products" designed by the Product Design Department, and they have to work within the rules by using "poorly made equipment" introduced by Production Engineering Department.
As you can see from the flow of stages 1~4, the further downstream you go from the Product Design Department-->Production Engineering Department-->Manufacturing Department, the heavier the load of upstream failures becomes.
To prevent this from happening, you have to maintain a high level of quality of work from upstream.
Introduction of each department job (Quality Assurance Department)
Finally, Quality Assurance Department. This department is the guardian of the company.
They manage internal change procedures, such as design changes and process changes. They never do anything themselves, but they complain loudly to other departments.
Negatives in Quality Assurance Department
Then there are the negatives.
Honestly, I can only imagine that this department is responsible for cleaning up the mess of other departments.
The main task of any company's quality assurance department is to handle customer complaints.
They explain to customers when quality problems occur and how to prevent them from happening again. (In reality, they only demand that Product Design Department, Production Engineering and Manufacturing Department take action.)
The rest of the work is incoming inspection and outgoing inspection work. The workload for these tasks is also lighter than that of manufacturing department. Incoming and outgoing inspections are sampling inspections of partial items only.
Even if accepted component at incoming inspection is found to be defective on the production line and needs to be sorted, it is the manufacturing department that does the sorting. From the point of view of responsibility, this is a strange situation.
If they really want to guarantee quality, they should be involved in the project at the early stages 1-3 and control quality upstream.
Unfortunately, most of the work in quality assurance department is at stage 4. Personally, it is the least attractive department.
That's all. I have introduced negative aspects of each department in manufacturing industry.
RELATED) Production Engineering Job Descriptions and Career Development
RELATED) Five benefits of production engineering job