Product traceability in the manufacturing industry
In this article, I'm going to talk about "Product traceability in the manufacturing industry". As a production engineer, I have come to realize how difficult it is to maintain and improve a production line. One of the reasons is the constraint of having to guarantee the quality of the products that are shipped to market (it's not just a matter of producing them, but maintaining production in a situation of great responsibility is very tough). In this article, I'll give you an overview of the process.
【content】
- Manufacturer Responsibility for Shipping Products in the Manufacturing Industry
- Introduction of common product traceability methods
- Level 1 Document management (complete manual record keeping)
- Level 2 Data Management (serial control for inspection processes only)
- Level 3 Data Management (serial management across almost the entire process)
- Benefits and Implementation Costs of DataMatrixCode (DMC)
- Estimated cost of DMC implementation and scanner reading accuracy
- Factors causing abnormal DMC readings
- Obstacle 1: Halation
- Obstacle 2: Lack of Margins
- Obstacle 3: Surface condition of the material
Manufacturer Responsibility for Shipping Products in the Manufacturing Industry
In the manufacturing industry, the product liability law imposes quality responsibility on the manufacturer for the products shipped.
If a product is shipped to the market with a serious quality defect, the manufacturer is responsible for the quality of the product.
Quality problems cannot be hidden, and if a defect is found, the manufacturer is responsible for recalling the product or shipping a replacement.
Some companies are looking to expand their business or increase their market share, but they are all subject to quality assurance. Low quality levels and the risk of market complaints will crush the company through business expansion because it also increases risk. The more you ship to the market, the more coverage you have when you have a market claim!
For these reasons, manufacturers in the manufacturing industry have adopted a system that allows them to guarantee the quality of their shipments and to filter out defective products (product traceability).
Introduction of common product traceability methods
The following is a brief introduction of production process.
The process consists of parts input, assembly, inspection, and shipment.
The important parameters at this time are parts, equipment and people.
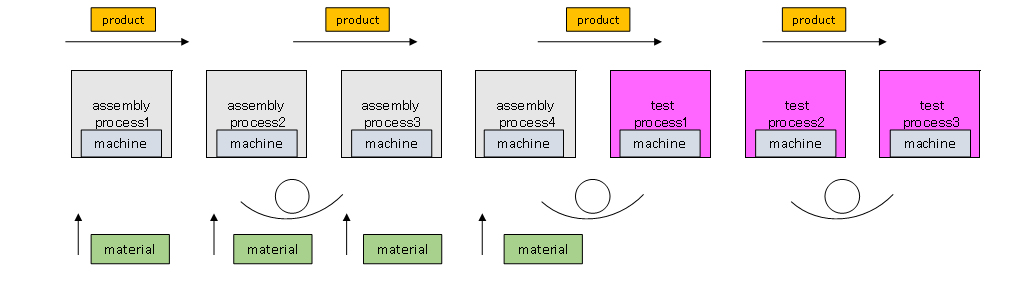
Next, I will introduce the methods of product traceability. There are three main types. Each of them has advantages and disadvantages in terms of introduction cost and filtering. In addition, depending on the products you handle, they may not be suitable for your production line.
Level 1 Document management (complete manual record keeping)
It is the management of the so-called 4M elements.
- Records of the workers in charge of the production day
- Equipment check records
- Quality record of the first product
- Lot records of materials used
These are recorded daily in a document and the document is stored.
The advantage of this traceability method is that it is not costly to introduce, and it has been a common method used by many companies for some time now.
However, there is a disadvantage. It is necessary to keep daily records and the amount of storage is huge.
The automotive industry requires that quality documentation be kept for 10 to 15 years after the product is manufactured (*This period may vary slightly depending on the requirements of the customer, but is at least 10 years).
When a problem occurs, the search process cannot be automated, even if you are trying to go back to the past records.
There is also the possibility that the document cannot be found. Even if you want to digitize the documents into PDF files, there are additional man-hours involved. Therefore, although it is easy to introduce, it is not easy to use and is not suitable for the long term.
Level 2 Data Management (serial control for inspection processes only)
Here is the second traceability method. This one is a semi-automated case.
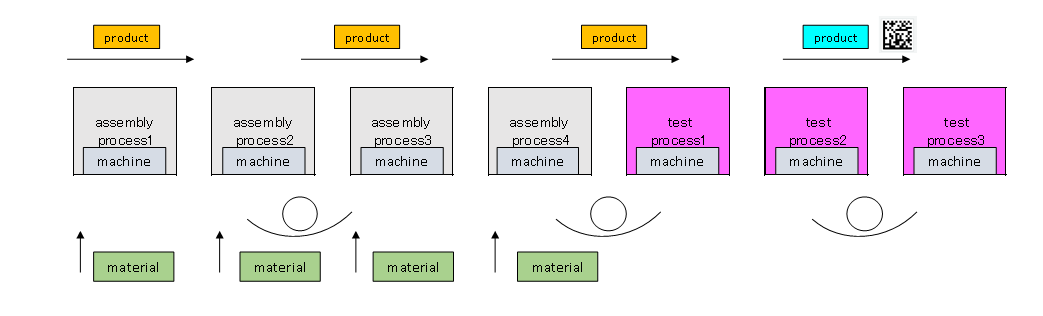
DataMatrixCode (DMC) has been added to the final product as shown in the figure. If you have one, you will be able to manage the individual inspection data for each product. Sometimes this is due to customer requirements, and sometimes it is for internal reasons. The DMC is simply the serial number of the product. For example, the following DMC has the information "200329A0300001".
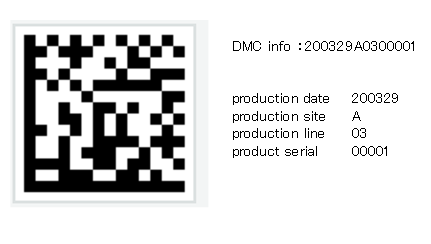
For example, if the serials show the production date, product serial, production line number, and location number, then the serials can be used to identify the production date and location.
Also, if the product serials and the inspection data of the equipment are stored together, it is possible to check all the inspection results later.
Compared to the Level 1 system, this system significantly reduces the workload of record searching and verification when a problem occurs.
In addition, once the inspection data is processed, statistical analysis can be performed immediately.
Level 3 Data Management (serial management across almost the entire process)
Next, let's take a look at the case where Level 2 DMC management is applied to the entire process. The concept is as follows. DMC is applied from the component level instead of the end product.
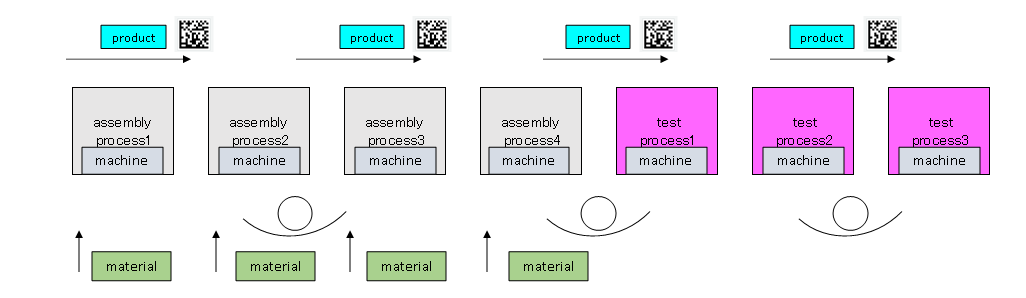
This increases the scope of quality control automation.
In addition, the data of material lots can be stored together with DMC information, allowing you to manage the information of input materials with serial information in addition to product inspection data.
While there are many advantages compared to Level 1, there are also disadvantages to this proposal. That is the high cost of implementation.
In terms of hardware, you need to purchase a DMC scanner and prepare a server. In terms of software, you need to set up a server environment and maintain it.
It requires an initial investment, and you have to train your people to handle that maintenance.
It is also necessary to have a system that automatically feeds back to the production line if there is an error in the data storage on the server, in order to avoid the situation where data is not saved from the middle of the process.
In some cases, problems such as production line stop due to data storage errors may occur. Even if there is nothing wrong with the equipment or product quality, there is still a chance that the production line will be stopped for reasons of in-house data management.
If you're a production engineer, you know how wasteful this stop is.
Benefits and Implementation Costs of DataMatrixCode (DMC)
Finally, here's a brief overview of DMC.
Implementing DMC in production line can be useful in many ways in terms of the work of production engineer, for the reasons introduced in Levels 1 and 2.
However, there are some negative effects of adding DMC.
For example, just as in the case of "production line stop due to a network error" described above,
production line can be stopped because "the DMC is not readable".
This is a waste of time and money, considering that the production line would not have stopped without the DMC.
Estimated cost of DMC implementation and scanner reading accuracy
Laser markers are used to engrave the DMC. Depending on the manufacturer, the estimated cost is between $20,000 and $40,000.
I've been a production engineer for many years, but I haven't had much experience with laser markers failing, and most of the equipment I've been able to use for nearly 10 years.
As for DMC scanners, the cheapest one is about $500. Some of the more expensive ones cost between $2,000 and $3,000.
The price of DMC scanner depends on the readability of the DMC.
If you want to engrave DMC on small area or on curved surface, you must use a high precision scanner.
Otherwise, a scanner that costs about $500 can handle the job.
Factors causing abnormal DMC readings
Here are a few factors that interfere with the DMC readings.
Obstacle 1: Halation
First of all, it's called halation.
As any engineer who has worked with cameras will know, this is when a part of the DMC is blurred by the reflection of the illuminated light.
When this happens, the scanner will not be able to recognize the DMC correctly.
The solution is to adjust the angle of the scanner.
However, if the DMC is engraved on a curved surface, this halation can be extremely difficult to avoid.
We recommend that DMCs be stamped on flat surface.
Obstacle 2: Lack of Margins
Next is the lack of margins.
There is a white margin around DMC.
These white spaces are important for proper identification of DMC.
If there is not enough space on the product to mark DMC, and if this margin is cut off due to misalignment or other factors, reading error will occur.
Try to leave enough margin when deciding where to engrave.
Obstacle 3: Surface condition of the material
The next is the surface of the material.
While this is not a problem for die-cast aluminum products, the surface condition of metal products such as iron and other processed or pressed products can change slightly due to discoloration of the cleaning solution after cleaning or during heat treatment.
Generally, product designers do not care about DMC stamping, and therefore do not specify the surface condition (since DMC is rarely introduced at the sample production stage before mass production, it does not appear as a problem).
However, once mass production begins, the effects of these disparate parts will occur. The only way to solve this problem is to make an agreement with the supplier.
RELATED) The risk of Mass Production in Manufacturing Industry
RELATED) Excessive Quality Inspection Doesn't Work
RELATED) Introduction of Pareto charts