Principles of TIG Welding and Issues in Mass Production
In this article, I talk about "Principles of TIG Welding and Issues in Mass Production".Based on my experience as a production engineer, I will focus on an overview of TIG welding and cautions during mass production.
TIG welding has been around for a long time and is inexpensive to introduce, but it is also true that there are parts of the technology that are not suitable for mass production processes.
【content】
- Background on the use of TIG welding
- Principle of TIG welding
- Advantages and disadvantages of TIG welding
- Initial evaluation and management of TIG welding
- Verification of welding parameters
- Quality control items after welding
- Concerns in the mass production process
- Durability of the electrode
- Effect of electrode replacement on cycle time
- no welding error
- welding short error
- Noise control
- Shield gas preparation
Background on the use of TIG welding
As mentioned in the resistance welding article, there are several ways to join metals together, including welding, press-fitting, caulking and soldering.
Press-fit and caulking are used for joining metals that are not energized, which require only mechanical joining.
Compared to welding, these methods are simple and quality control is easy.
Welding is used for joints where press-fit and caulking cannot be used or where strength is required at high temperatures.
However, since TIG welding melts metal by the principle of lightning, fine control is difficult and the electrodes are not durable.
Principle of TIG welding
The outline of TIG welding is performed using a shielding gas to shield the weld from the air.This is to prevent deterioration of the weld zone due to oxidation.
As shown in the figure, voltage is applied to the electrodes and lightning is discharged from the tip of the electrode.
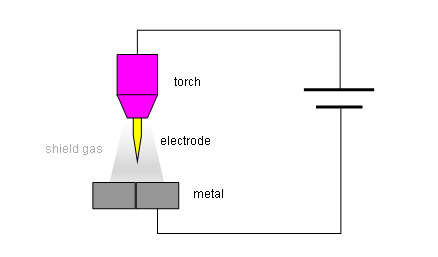
The schematic diagram shows a flat metal plate, but considering the concentration of electric fields, a sharp tip is more suitable for TIG welding than a flat one.
Advantages and disadvantages of TIG welding
The advantage of using TIG welding is that there are few space limitations. The electrode tip can penetrate into small areas, making it suitable for joining small areas.
In addition, the technology itself has been around for a long time and has the advantage of being inexpensive to install.
Much higher installation costs are required when using laser or other joining methods.
On the other hand, the disadvantage is that they are not durable.
As you will see if you use it continuously, the electrode tips need to be kept sharp, and the wear and tear of the electrode tips will affect the quality of the weld.
It is necessary to grind the electrodes frequently with electrode polishing grinder. Another disadvantage is that it is difficult to control the welding position.
As mentioned above, the welding position is determined by the principle of lightning strikes, so it is not easy to predict the position to be welded.
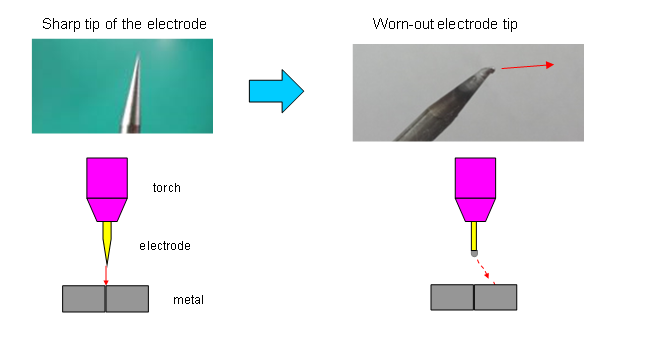
Initial evaluation and management of TIG welding
Depending on the weld location, if it's just a rigid fixation, it's only guaranteed to satisfy the strength after welding. When welding conduction part such as terminal and copper wire, the weld appearance, electrical characteristics after welding, and withstand voltage characteristics of the surrounding area should be checked (whether or not the insulation has been destroyed) and so on. The following are some of the key points that a production engineer should focus on
Verification of welding parameters
The method for evaluating welding conditions is the same as that presented in the resistance welding article. The main parameters will be the welding time, welding current, and the distance between the electrode and the weld.
Quality control items after welding
The quality judgment items depend on the weld location. Weld appearance, weld strength, electrical characteristics after welding, and withstand voltage characteristics (insulation characteristics) of the surrounding area. Since there is a possibility that weld spatter may be emitted in the surrounding area, it is necessary to confirm the presence of such spatters when welding at a location where metallic impurities are not desired to be generated.
Concerns in the mass production process
In consideration of the above, let's take a look at some of the points that production engineers should be aware of in mass production.
Durability of the electrode
I have examined the angle of the electrode tip and the distance between electrode and the welded material in various ways.
The results showed that it is better to use a sharp electrode tip with 15-degree angle, and when the electrode tip is worn out, to push it out and use it continuously, with minimal loss in total.
※ However, if you overdo it, the positioning will fail and increase your downtime.
It depends on the structure of the device and the rule of thumb as to whether it is more advantageous to replace the electrode or to keep pushing it out.
Effect of electrode replacement on cycle time
Depending on the number of welds in a cycle, this frequency of electrode changes worsens the cycle time that was originally expected.
My old welding equipment required electrode changes every hour. Even if it's 3 minutes, you will certainly lose 3 minutes of your 60 minutes. That's a 5% loss in operating time.
If this welding process is not a bottleneck in the overall production line, then you won't have to worry about electrode change loss time.
If the welder is a bottleneck process, then electrode change loss time will have a significant impact unless improvements are made to reduce cycle time.
no welding error
A metal mesh is attached to the inside of the nozzle for noise reduction. We also wrapped a ground wire around the ceramic nozzle as a noise countermeasure. All of them are recommended by the welding power supply manufacturer.
welding short error
This is the opposite of an accidental fire. If the electrode tip comes into contact with the weld, the arc cannot be generated, resulting in a welding error. Thus, delicate positioning of the electrode tip is required, but the electrode tip can quickly wear out or foreign objects can stick to the tip and the positional relationship is lost. Unfortunately, this is the limitation of TIG welding.
Noise control
This may have been due to the poor quality of the welding power supply I used, but I was bothered by the malfunctioning of the welding power supply. The resistance welders never had any noise malfunctions, but the TIG welding equipment frequently caused no-welding-error and power errors. As mentioned in the manual for the welding power supply, we had to wire the ground wire separately and shield the torch and ground electrode wiring from noise.
Shield gas preparation
In order to supply shielding gas to be consumed in welding, a gas tank must be prepared around the equipment. Gas cylinders can be rented, but if they are not replaced before they run out, the mass production process will be stopped due to lack of shielding gas. If you want to avoid replacing gas tanks, it is possible to install a slightly larger gas tank outside the plant and run pipes from there, but this will require an initial investment.
RELATED) Overview of vision system (Principle of edge detection)
RELATED) Introduction of caulking process
RELATED) Introduction of resistance welding