The Advantages of Winding Machine Manufacturers
In this article, I'm going to talk about "The Advantages of Winding Machine Manufacturers". As a production engineer, I have many opportunities to handle mass production equipment. Among them, I will introduce a special type of equipment, the winding machine.
What is winding machine?
A winding machine is a piece of equipment used to wind copper wire around component. The main difference between this equipment and other equipment is that the parts (copper wire) it handles are not rigid. Special techniques are required for assembling parts that are not rigid.
There are various winding methods depending on the wire diameter of the copper wire and winding type. There are thin wire winding machines used in electronic components and thicker wire winding machines used in automobile parts. Depending on the product winding specifications, there are various winding methods such as nozzle winding, flyer winding, split core winding, inserter winding, etc.
By the way, in the winding machine industry, the impression is that Japanese manufacturers of winding machines are leading the world.
It is one of the few Japanese industries that are doing well against the rest of the world in the manufacturing industry.
The Market Demand for Winding
Since every product that utilizes electromagnetism has a coil in it, the demand for winding machines is expected to grow in the future along with the demand for electronic components and automation. For reference, the following is the market price trend of copper. Specific product groups include automotive electrical components, industrial motors, home appliances, power devices, and information and communications equipment.
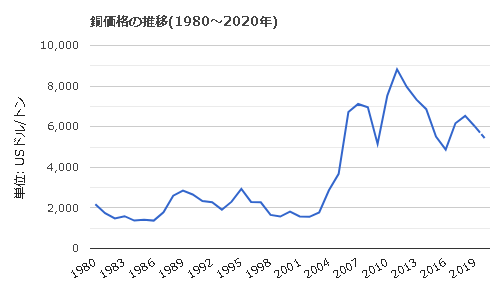
ref)世界経済ネタ帳 https://ecodb.net/commodity/copper.html
Technical Advantages of Winding Machine Suppliers
The demand for the winding machine itself seems promising, but unlike general equipment, there is a high barrier to entry for winding machines.
In my opinion, there are three advantages of a winding machine supplier, "tension control", "high-speed servo control technology", and "film removal technology".
tension control
As mentioned earlier, copper wire is not a rigid body.
Due to its unstable shape, the winding operation must be performed under a constant tension in order to achieve a precise winding operation.
If the tension is too weak, it causes disordered winding, and the shape of the finished coil becomes unstable.
If the tension is too strong, the copper wire is stretched, and the copper wire resistance and magnetic characteristics become unstable.
This tension control is a special technology and cannot be easily duplicated by ordinary equipment suppliers. Winding machine suppliers have developed their own tension controllers.
high-speed servo control technology
One of the requirements of a winding machine is the cycle time.
Although consistent winding quality is a primary requirement, unlike other equipment, the winding operation takes longer. While the press-fitting and caulking operations can be completed in 5 to 10 seconds, the winding process takes more than a minute. When considered in a normal mass production process, it is difficult to achieve a good balance with other processes, and reducing the cycle time of the winding process is a major factor in increasing productivity.
The process of winding unstable copper wire at high speed requires high-level servo control technology. To understand the difficulty level, imagine controlling multiple axes simultaneously at high speed, including XYZ and rotational motions.
film removal technology
Lastly, the film removal technology. After the copper wire is wound, the copper wire coating is stripped off. The purpose of this is to secure the electrical conduction area to be joined to the terminals at a later process in order to allow the current to flow through the coil (*stripping may not be necessary in some cases).
The operation itself is simple, but it is not easy to operate stably. The following are examples of failures. The blade slips and the peeling cannot be performed properly, the durability of the peeling cutter is not sufficient, peeling debris cannot be collected, or impurities are left behind that cause scratches on the normal wire coils, and so on.
These three items have been developed independently by the winding machine suppliers themselves. This is the advantage of winding machine supplier. It's not like you can buy a commercial product to make the same kind of winding machine, which is why it's difficult for other equipment suppliers to enter the market.
The original development of winding machine supplier and problems for production engineers
While it is true that developing original core technology is the advantage of winding machine supplier, it is also a concern for the field-level production engineers who are the users of winding machines.
The PLC control and servo control are completely different, which makes it different from other equipment. Because of this, production engineers have to learn the technology specifically for the winding machine.
In fact, this hurdle to learning the technology is one of the advantages of winding machine suppliers. If they can reach new customers, it means they are more likely to get repeat customers in terms of operation. You don't want to buy a new winding machine from another vendor that requires you to learn different skill after you've taken the trouble to learn it. There is also the advantage of selling multiple units due to the long cycle time.
RELATED) Overview of vision system
RELATED) Introduction of caulking process
RELATED) Introduction of resistance welding