Introduction of Manufacturing Floor Management and Skill Map
In this article, I'm talking about "Introduction of Manufacturing Floor Management and Skill Map". As a production engineer, you need to have a deep understanding of how the manufacturing floor works and how it is managed. Because problems occur every day on the manufacturing floor, in addition to process design and equipment, the concept of site management is also important. So, I'm going to outline a manufacturing floor skills map that definitely help production engineers on the job.
【contents】
- What is the manufacturing floor skills map?
- Case study of bad skill map management
- Skill map does not reflect reality
- Not accompanied by training activities to fill out the skills map
- No identification of critical processes on the skills map
- How to manage the manufacturing floor successfully
What is the manufacturing floor skills map?
A skills map is a summary of where operators are located and their corresponding skills on the manufacturing floor. It is a common management method in the manufacturing industry.
Specific Examples of Skill Map
Here's one specific example.
Suppose there is a production process like following.
There are five operators. Here is a skill map of six workers, including one field supervisor.
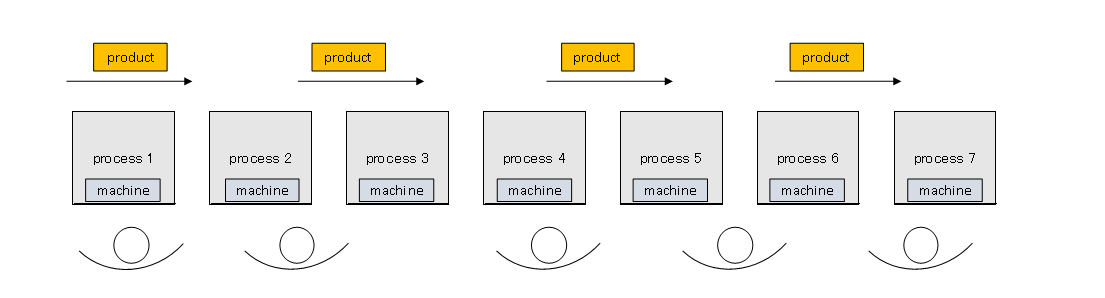
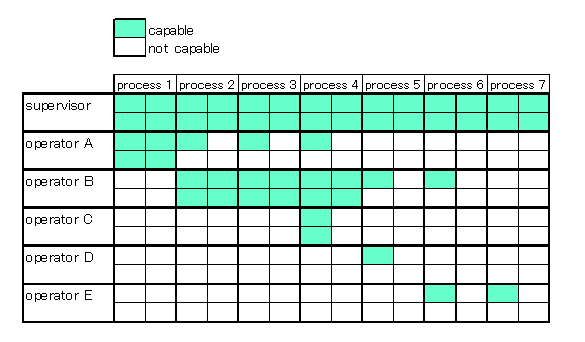
As you can see from this table, preparing a skills map visualizes the level of skill of the operator in each process. This can be posted at the side of the production line so that the supervisor knows at a glance who and where to put them. This way, you won't have to waste time worrying about placement or re-training them.
Case study of bad skill map management
Managing a skills map seems like a simple task, but there are manufacturing sites that don't manage it well. If a company has high turnover rate or process design takes a long time to train, they are struggling just to manage their operators.
Each region has its own unique challenges in terms of turnover, as it is influenced by cultural factors and economic trends in the region. Depending on the organizational structure and company's situation, people may be too busy with their extra work to do the work they should be doing. When this happens, it's a negative spiral. Here are a few examples of bad skill map management.
Skill map does not reflect reality
There's a skills map to the extent of "I prepared it because I was told to", but it doesn't reflect reality and it's not updated, etc. A common skill map is the one that summarizes only reality (a skill map with many missing teeth) and has no ideal state to aim for.
For example, there is a situation where no one else can cover the process if a particular operator retires. Even in these cases, there is not even training plan to increase the number of multi-skilled operators. This makes it hard to know why you are keeping a skills map.
Not accompanied by training activities to fill out the skills map
Depending on the capabilities of the production floor supervisor, it may not be possible to create and implement a medium-term training plan. In such sites, the same workers are always in charge of the same areas. (A week is all it takes to train a specific process, though...)
*Since the process is originally designed so that anyone can do it, it basically doesn't take long to learn, as long as the process is not related to special characteristics.
From supervisor point of view, there is a short term advantage of using the same operator for the same process, as it is more convenient and easier to manage. However, if a vacancy occurs, there may be a work process that no one can handle.
This not only increases production losses, but also increases the quality risk.
In order to eliminate the risk of vacancies, you have to make sure that multiple workers are available to cover many processes. The idea is to take preventive measures while you can afford it.
No identification of critical processes on the skills map
In every production line, there are key critical processes.
Special processes that deal with special characteristics, such as caulking and welding, are important processes, and there are also other processes that take time to learn and require skillful quality judgment.
Such processes need to be prioritized over other processes to increase the number of skilled workers. However, we often see manufacturing sites that that treat it the same as other processes.
It is possible to find temporary operators for simple work processes, but those critical processes raise the hurdle a bit. Some processes are difficult to handle in sudden situation, so you need to be aware of those critical processes.
How to manage the manufacturing floor successfully
My own suggestion, having seen a lot of manufacturing sites, is that there should be incentives for workers on the manufacturing floor. Most companies should have their salaries set at a flat rate.
Most companies will not change their salary even if they work hard or slack off.
It's a common way of thinking in Japan that says, "You're getting paid, so you should work properly".
This idea may be effective in Japan because the turnover rate is low and many people continue to work despite their frustration.
In other countries, however, this concept does not work.
In foreign countries, serious people tend to quit. They don't want to work with the same treatment when they see the workers around them slacking off.
When this happens, productivity and quality control on the production line worsens because useless people remain in the company. It's fatal to the company.
Considering these circumstances, we give incentives to people who work hard so that they don't suffer. For example, you could choose a few people per line who worked hard in the month and give them an extra benefit, or offer them a meal voucher for the cafeteria.
One way is to get them to learn new job and promote them. There are many managers who want to hire talent from the outside, but there are people within the company who can do an excellent job. It is important to create a system that keeps employees highly motivated to work.
RELATED) Introduction of Control Charts that Production Engineers Need to Understand
RELATED) introduction of product traceability in the manufacturing industry
RELATED) Equipment specifications that benefit cycle time and operating rates