Introduction of Control Charts of manufacturing site
In this article, I will talk about "Introduction of Control Charts of manufacturing site". As a production engineer, there are many things that you should know in addition to equipment problems and defective improvements. I will outline the control charts for process control and introduce key points for creating them.
What is a control chart?
There are various types of control charts. This time, I will introduce frequently used X-R control charts.
Control chart is a method for statistically monitoring process variability.
It is a tool for early detection of irregularities by analyzing statistical trends, which is used in the control of critical processes such as special characteristics. Separate from the normal product standards, a new control range (UCL, LCL) will be set and operated within that range.
Common situation for production engineers
It is a very common tool in manufacturing. However, with the exception of the production department managers and production engineering experts working on the manufacturing floor, most of the production engineers I've seen so far seemed to have a limited understanding of control charts, recognizing them as little more than sheets recorded on the manufacturing floor.
Specifically, the following are the situations
- They don't understand what the control chart is for in the first place.
- Unable to create a new control chart.
- They can't judge the abnormality.
Procedure for creating control chart
Now let's take a quick look at how to create a control chart. It's quite easy if you understand the content.
1. Prepare sample data
(Guideline: about 100 data consisting of 20-25 subgroups with a sample size of about 5)
*Data collection in subgroups across part lots, production times, etc. is recommended.
2. calculate the average value X and range R
First, we calculate average and range for each subgroup, and then we calculate average X and range R for the whole.
3. Determine the UCL and LCL.
*The detailed calculation method is omitted.
4. fill in the average value X, range R, UCL and LCL in the control chart format
The overall process is as described above.
The main task of creating a control chart is tasks 1 and 2. If you have this data, 80% of it is as good as completed.
Attached is a sample that shows the outline of tasks 1 and 2.
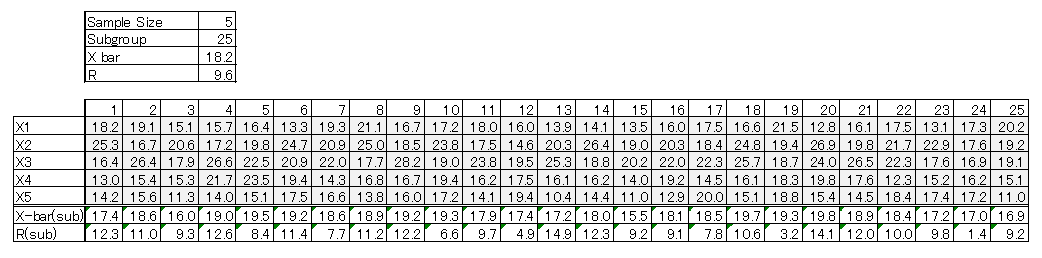
Control Chart Points
Points to focus ( abnormal trends)
- Abnormal trend 1: Control limit line (LCL, UCL) is exceeded
- Abnormal trend 2: Seven consecutive points (series) on one side of the center line.
- Abnormal trend 3: There are seven points (series) that increase or decrease in succession.
- Abnormal trend 4: There are far more points in the middle 1/3 of the control limit range than in the other 2/3.
- Abnormal trend 5: Far fewer points in the middle 1/3 of the control limit range than in the other 2/3

There were many production engineers who visually recognized Abnormal Trend 1 as abnormal, but there was little understanding of the other trends. You may not use control charts in your daily work and may not have a need for them in your work, but they are obviously something you should know as production engineer.
If you don't make a intentional effort to learn it, you won't be able to understand it forever. Some manufacturing sites may not use control charts to manage statistics.
If you are not operating correctly, this will definitely be pointed out in customer audits. A strict auditor will ask you if you understand how to manage the control chart itself.
Some companies posted anomalous trends on their control charts. This way, you don't have to go to the trouble of training operators, they will always have a guide to help them learn what the abnormal trends are naturally.
RELATED) Introduction of Manufacturing Floor Management and Skill Map
RELATED) Introduction of OEE, the production line operating rate indicator
RELATED) Outline of correlation evaluation methods for test equipment