Overview of 5-why Analysis at manufacturing site and its advantage
In this article, I'll be talking about the topic of "Overview of 5-why Analysis at manufacturing site and its advantage".
If you're a production engineer, you've probably experienced this at one time or another with quality issues for your customers.
Once you develop this approach, you can organize the flow of cause and effect and logic. As a result, you will surely improve your usual work efficiency.
What is the 5-why analysis of the manufacturing site?
First, let's outline the 5-why analysis.
5-why analysis is a method for asking yourself "why" about a problem that has occurred, to understand the true cause of the problem.
Originally, this method was used in Japanese manufacturing industry, but it is also commonly used in overseas manufacturing site.
To give you one example, let's do 5-why analysis when there is "TRAFFIC SIGNAL IGNORING" problem.
- Why 1: Why did you ignore the signal --> Because I was going to be late.
- Why 2: Why were you going to be late --> Because I overslept.
- Why 3: Why did you oversleep --> Because the alarm didn't go off. And so on, you dig deeper into the problem.
How to use 5-why analysis
Like FTA and Pareto diagrams described in another article, they are useful tools for solving problems on the manufacturing site, but their most common use is for reporting customer complaints when they occur.
Unfortunately, most people don't use 5-why analysis in their everyday work.
It's only when an external quality issue arises and the quality assurance department gets into a tizzy that they begin to prepare 5-why analysis for reporting.
It is very useful for analyzing and explaining the causes of problems in a sequential way (so it is used for customer reports).
On the other hand, a common mistake is a leap in logic or a lack of convincing causal relationships, and the document quality depends greatly on level of creator.
Sometimes it can even be manipulative material to hide inconvenient information.
The purpose of this article is to give you an overview and to help you use it in practice. You don't have to report it to others, just see it as a way to organize your thoughts.
Again, the goal is not to do it formally, but to train yourself to properly organize the causal relationship of things.
Specific Examples of 5-Why Analysis
Here's one specific example.
Let's try 5-why analysis in the case of press-fit process in which press-fit load abnormality occurred due to dry surface of component.
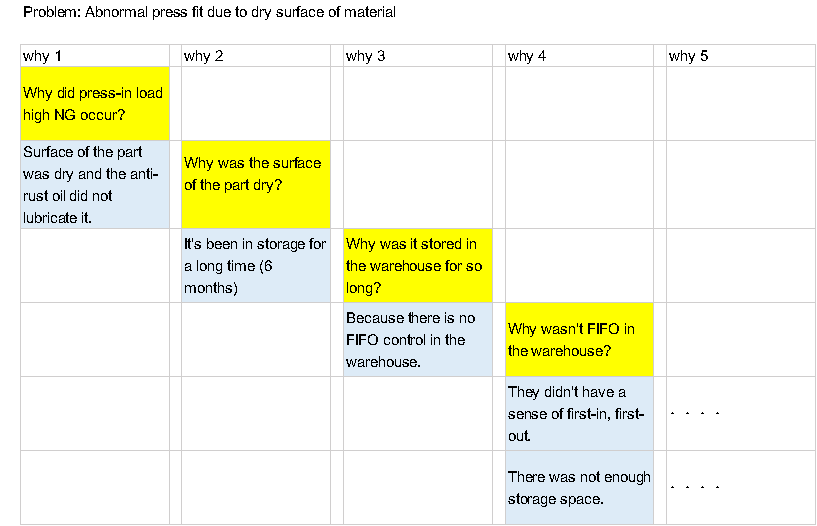
A simple example would look like this.
There are other factors, such as what the packing specifications of the parts and the results of the transport tests were, and whether the condition of the anti-corrosion oil was indicated on the drawings in the first place, but these are omitted here.
In the actual 5-why analysis, try to dig into the real cause of the problem.
The point of implementation is that the causal relationship before and after is correct and there are no leaps in logic.
If you're unsure, it's one thing to ask others to look at it and ask for their opinion.
Use as an analysis of general problems
I've outlined it briefly, but here's the main point of the story.
As anyone who has ever taken 5-why analysis seriously, for example in quality issues for customers, will understand from experience, this method of analysis is very useful in terms of correctly organizing the flow of logic.
This is because it allows us to sort out the cause and effect of the problem and to understand the problem in a structured way.
It is such a useful tool that it would be a shame to use it only for customer reports to analyze problems on the manufacturing site.
Try to keep this way of thinking in mind as a hint for casual, everyday tasks and difficult problems.
I'm not asking you to do 5-why every time, but rather to approach your work with the question of why it's happening.
Why are these equipment specifications like this?
Why can't my staff handle their work well?
Why do the upper management talk so long?
Why aren't they more productive?
Why isn't overtime being reduced?
If you can think objectively about "why" of your daily life and capture the true cause, you will be able to work more efficiently in your work.
The above is "Overview of 5-why Analysis at manufacturing site and its advantage".
RELATED) Introduction and Use of FTA
RELATED) The need to properly understand the essence of problem and common misunderstandings
RELATED) Problem Analysis Methods for Manufacturing Sites (Use of Histogram)