Introduction of OEE, the production line operating rate indicator
In this article, I will talk about the topic of "Introduction of OEE, the production line operating rate indicator". As a production engineer, it is important to have a correct understanding of production line productivity. In order to increase the productivity of the production line, I am going to give you a brief overview of OEE.
【content】
- What is OEE, the overall equipment efficiency of production line
- Specific Examples of OEE
- OEE Improvement 1) Factors of quality loss and countermeasures
- OEE Improvement 2) Factors of availability loss and countermeasures
- OEE Improvement 3) Factors of performance loss and countermeasures
- The key to increasing OEE of production line
What is OEE, overall equipment effectivenes of production line
OEE, or Overall Equipment Effectivenes, defines production efficiency in terms of Availability, Performance and Quality.
The formula is OEE = Availability x Performance x Quality
All companies use this as an indicator to measure the performance of their production lines, and 85% is a common target value.
The company I used to work for targeted 85% as 5% availability loss (loss due to pre-operation inspection, etc.), 5% performance loss (equipment stop and downtime), and 5% quality loss (loss due to line defect rates).
Specific Examples of OEE
Let me give you one specific example.
Suppose the results were as shown in the following table during the 6:00-7:00 time period.
The availability is 100%, meaning that there was no downtime at all.
Performance was 92.8%, slightly below plan. For quality, two units are defective, which is 98.8% of achievement.
The OEE calculated from these three factors is 91.7%. As you can see, analyzing the OEE makes it easier to understand what is causing the loss.
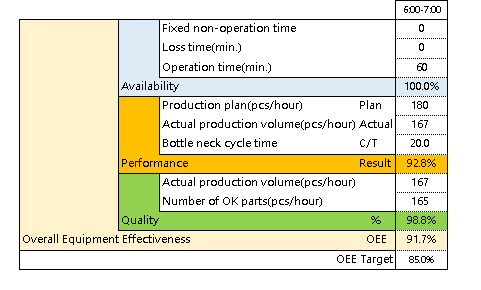
In this example, high OEE is achieved, but this is not the case on the real production line. Even in the production line that has been in mass production for several years, it is not easy to maintain consistent 85% OEE. Here are some of the factors that worsen OEE and what can be done about them
OEE Improvement 1) Factors of quality loss and countermeasures
First is quality factor of OEE.
This is discussed in another article, but the goal of a production line is to have a defect rate of 1% or less in terms of scrap value.
If the quality loss on OEE is greater than 5%, production numbers will not increase unless the defect rate on the production line is improved.
You have no option but to take effective countermeasures according to the details of each defective item, such as equipment factors, material factors, design factors and oepration factors.
reference)Parate-analysis、FTA Analysis
OEE Improvement 2) Factors of availability loss and countermeasures
The second is OEE availability loss.
This is the loss time that is not available for production during operating hours.
For example, pre-operation inspection time at the beginning of shift is time that cannot be used for production.
Other sources of loss are when there is a general conference or when the daily meeting time is conducted within the available hours.
On the other hand, by running equipment during planned outage time (e.g., breaks), you can temporarily make up for any losses that occur during the day.
The same reason applies to production on weekends to gain operating time.
OEE Improvement 3) Factors of performance loss and countermeasures
The third is performance loss.
This is one of the most relevant factors of OEE loss to production engineers.
This performance loss is often caused by downtime and equipment stop.
Losses are caused by the failure of the equipment to operate stably.
As a production engineer, this may sound like a headache, but there are a few key points to consider.
To avoid losing OEE, you need to focus on the bottleneck processes.
Even if other equipment is a little unstable, as long as the bottleneck processes operate stably on cycle time, the output will not be that bad.
It is important to pay attention to the operating rate of the bottleneck process and minimize losses (such as equipment stop) in the bottleneck process as much as possible.
Even if there is no equipment downtime, the output will not improve if the equipment is idle, so it is important to continue to feed in materials from the previous process so that the equipment in the bottleneck process does not have to wait.
The key to increasing OEE of production line
Finally, here are some points that will increase your OEE.
The idea is to keep track of your production performance against your plan every hour until your OEE is stable.
And keep track of what causes the underachievement.
Start by achieving even a few times during the day when production line can achieve the plan.
Once you have achieved that goal, you will gradually see the cause and points of improvement.
Whether it's the high number of equipment downtime, logistical issues in the production line, defect rates, operating hours, or some other factor, as you take the data and analyze the problem in detail, the output will gradually increase.
That's just a brief overview of OEE in the production line.
RELATED) Equipment specifications that benefit cycle time and operating rates
RELATED) The need to properly understand the essence of problem and common misunderstandings
RELATED) Overview of 5-why Analysis at manufacturing site
RELATED) Introduction of Pareto charts